[ad_1]
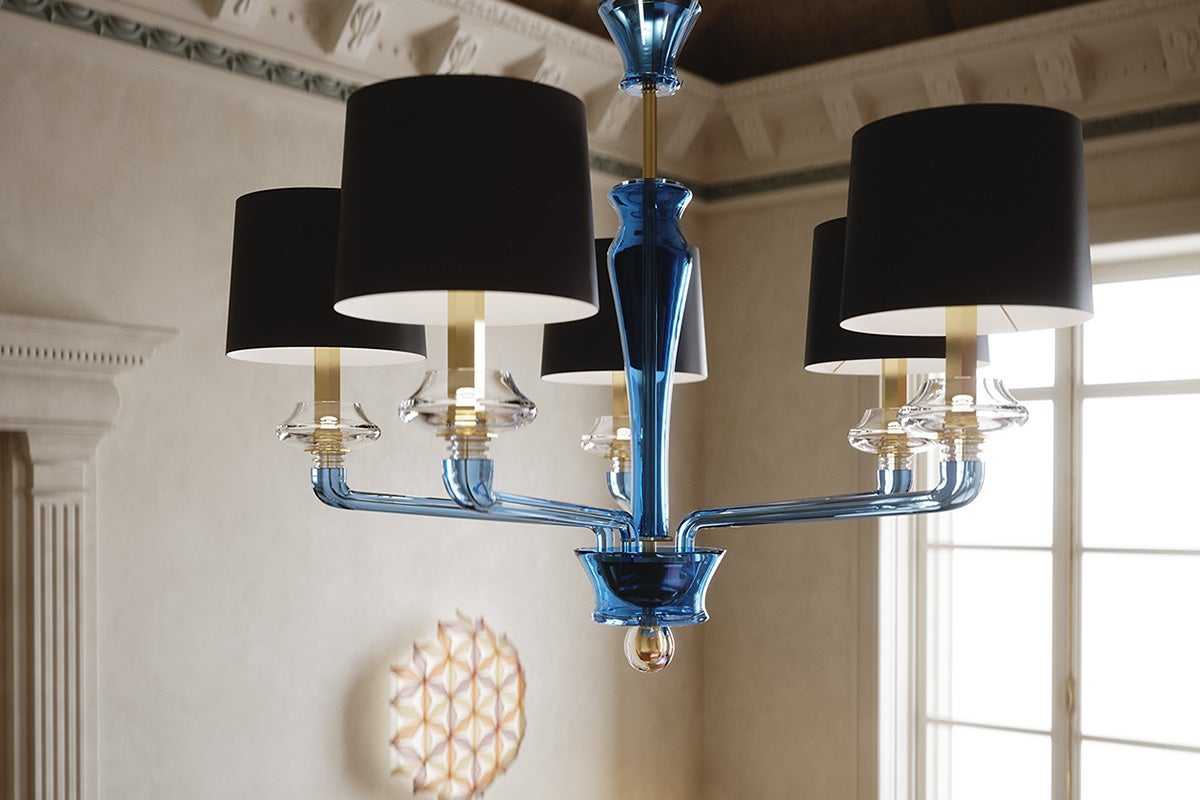
The furnaces never sleep. Steps from Murano’s quiet canals they rage at 1,400 degrees Celsius, guarding 725-year-old secrets: The meticulously measured combinations of sand and precious minerals behind Barovier&Toso’s prismatic glassworks.
Each week, some 3,000 to 4,000 pounds of Partia–precise glass recipes–are melted, blown, twisted, and polished here on the Rio dei Vetrai, Venice’s river of glassmakers. It’s a rhythm that has flowed through Barovier&Toso’s workshop since 1295, expanding and cooling over 20 generations with one constant: The emergence of awe-inspiring crystal from the flames.
Renaissance Beginnings
Like most stories, the tale of Barovier&Toso began with being in the right place at precisely the right time. Ideally situated between Central Europe and the Adriatic Sea, the Kingdom of Venice reached its apex during the early Italian Renaissance by establishing itself, arguably, as the Silicon Valley of its era—but with silica. By mastering the complexities of artisanal crafts like glass and Mediterranean waterways, the Venetians’ prowess for technology and luxury goods–and the resulting profits–defined local politics.
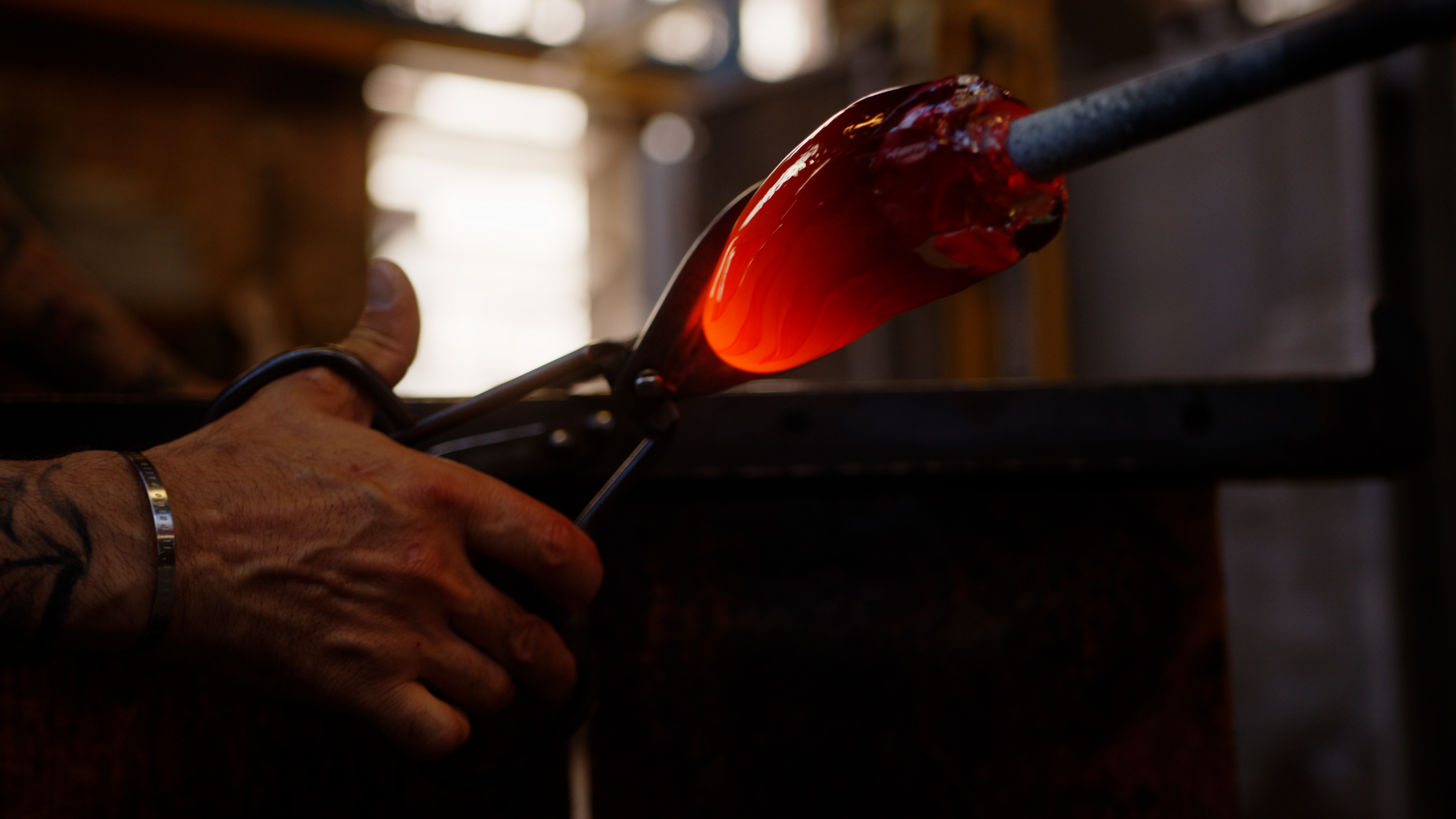
Eager to guard their secrets and prevent foreign competition in the glass market, the Venetians created highly specific legislation to regulate glass production. First, they mandated that all glass furnaces–and thus glassmaking workshops–be moved away from central Venice and onto the nearby island of Murano, creating the moniker “Murano glass.” In print, they reasoned the move would prevent potentially devastating fires within the primarily wooden city. In practice the law isolated glassmakers, making it harder for their techniques and precious Partia to be stolen and replicated outside Venice.
The Venetians simultaneously recognized the need to encourage glassworkers to ensure the lucrative trade remained, so they offered glassworkers near-noble status in the kingdom. In fact, the daughters of glassworkers were even allowed to marry into noble families, inspiring glassworkers to establish multi-generational glassworks.
This was the Venice where young Jacobello Barovier came of age, migrating to Murano and, according to 13th century documents, establishing himself as a “glass master.”
Crafting Classics, Century-In & Century-Out
Following Jacobello’s lead, each subsequent generation of Baroviers continued tinkering in the workshop, leading to renowned advancements in mouth-blown glassware. Angelo Barovier, the rare glassworker who combined artistry with scientific education, consistently experimented in the workshop, eventually creating what his counterparts considered impossible: perfectly transparent glass. Known as cristallo, the clear and luminous glass now referred to as “Venetian Crystal,” is as brilliant as leaded crystal but made without lead or arsenic. For centuries, the Barovier family was the only glassware maker allowed to forge cristallo, and Angelo continued to innovate creating lattimo and chalcedony glass in addition to the famed Barovier wedding chalice.
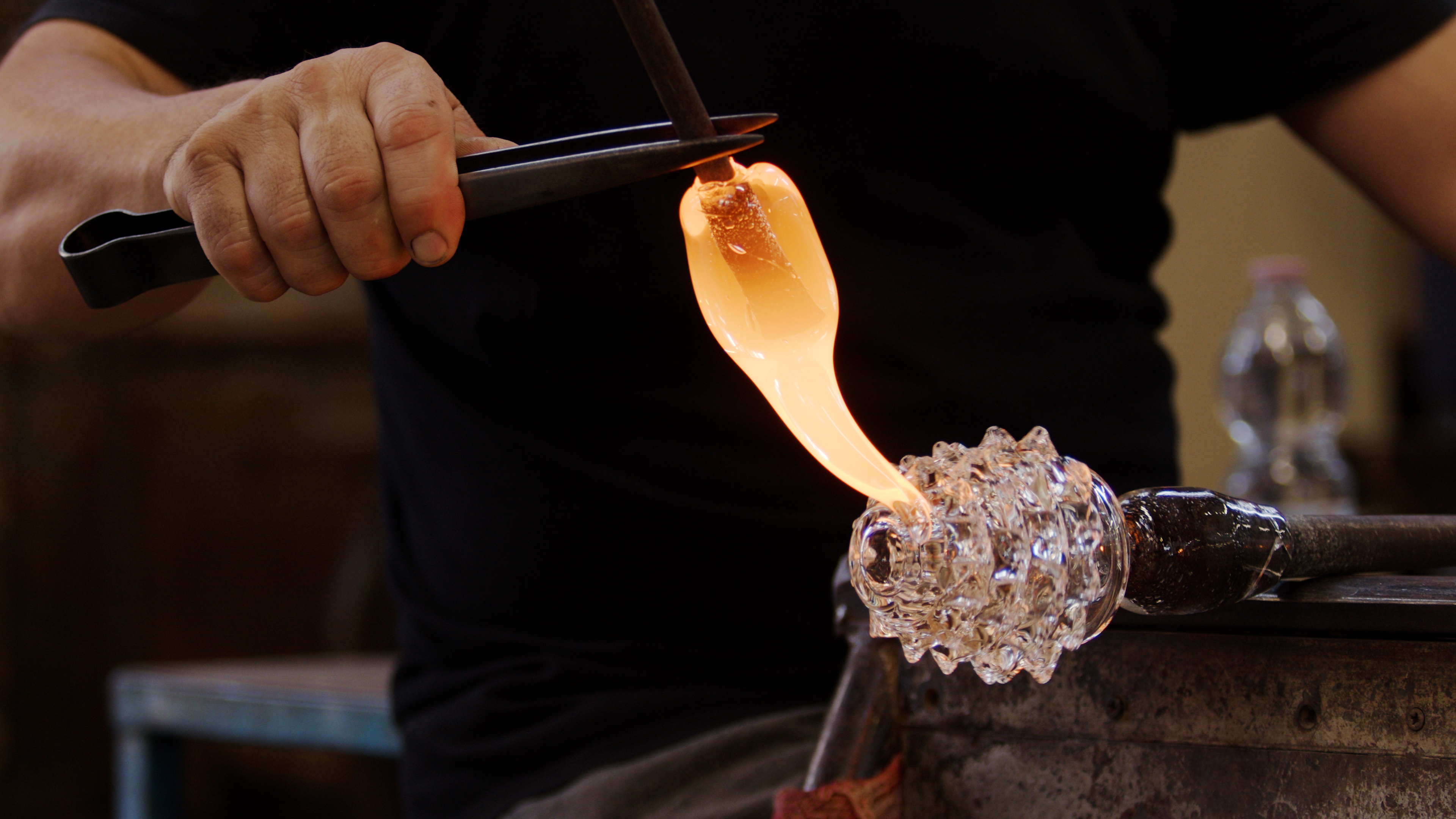
To this day, every product with the Barovier&Toso stamp is still produced completely by hand using long, hollow metal rods and roughly the same simple tools. Moving like metronomes from furnaces to cooling ovens and molds, each glass master–most of whom apprentice for 20 years–works with an assistant and several apprentices to blow, turn, and pull each piece into the perfect form, working without interruption as the molten sand becomes firm and eventually rigid. The impossible twirls and delicate designs of each piece are shaped and pulled with small hand-held pliers, hammers, and grinders.
The myriad permutations of fusing sand and minerals into glass–to say nothing of the endless creative options for decoration–allowed the Baroviers to continue innovating even after Venice’s golden age. Despite protectionist policies and Napoleon’s invasion–which outlawed the glass trade temporarily–Barovier’s furnaces blazed.
In 1896, as the glass trade was recovering, Giuseppe Barovier and his brothers re-named their workshop Artisti Barovier, setting the stage for the family’s modern resurgence. Considered an artistic prodigy, Giuseppe developed the murrine, or mosaic, technique that defined luxury Murano glassworks for decades. Layering colored glass together, the murrine technique ensured Barovier works were identifiable, as did the crest that Artisti Barovier created.
During this era, Giuseppe and his brothers also arguably invented modern Murano glass as we know it today: Artistic, elegant pieces defined by their ethereal lightness, whereas traditional glass works had been characterized by weight and practicality.
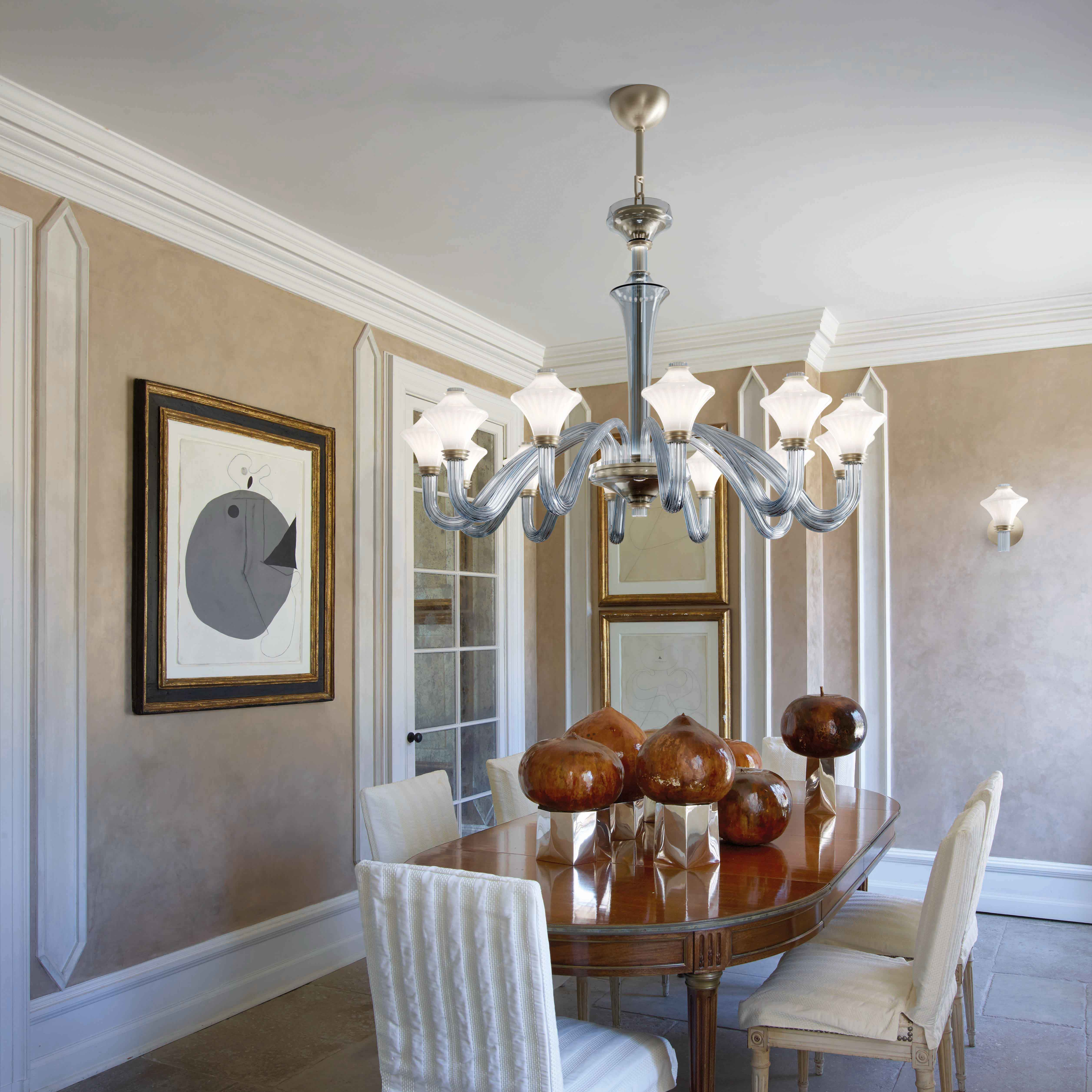
Expanding on Guiseppe’s enterprising spirit, his nephew Ercole expanded the Barovier legacy into the 20th century. Ercole and his brothers led the merger between the Barovier and Toso families in 1936, creating the Barovier&Toso powerhouse we know today.
Ercole rapidly became the beating heart of Barovier&Toso and creating over 23,000 pieces. In his 50 years at the helm, Ercole designed the process and the pieces for the mythical Primavera and Rostrato collections, distinguished by their gravity-defying shapes and inimitable patterns. The Rostrato technique, where molten glass is delicately pulled with pliers to create delicate peaks on fixtures, vases, and glassware, has become a defining technique for Barovier&Toso.
The one-of-a-kind Primavera pieces, where hairline cracks create a cobweb-esque pattern, have since become some of the most highly sought-after glassworks in the world. Now fetching over $300,000 at auction, no other glassmaker has ever been able to successfully replicate Ercole’s technique.
Shaping A Renaissance Legacy for the 21st Century
Ercole’s reality-distorting masterpieces paved the modern path for Barovier&Toso, who began creating commissions for palaces, museums, and luxury designers before retiring in the 1970s.
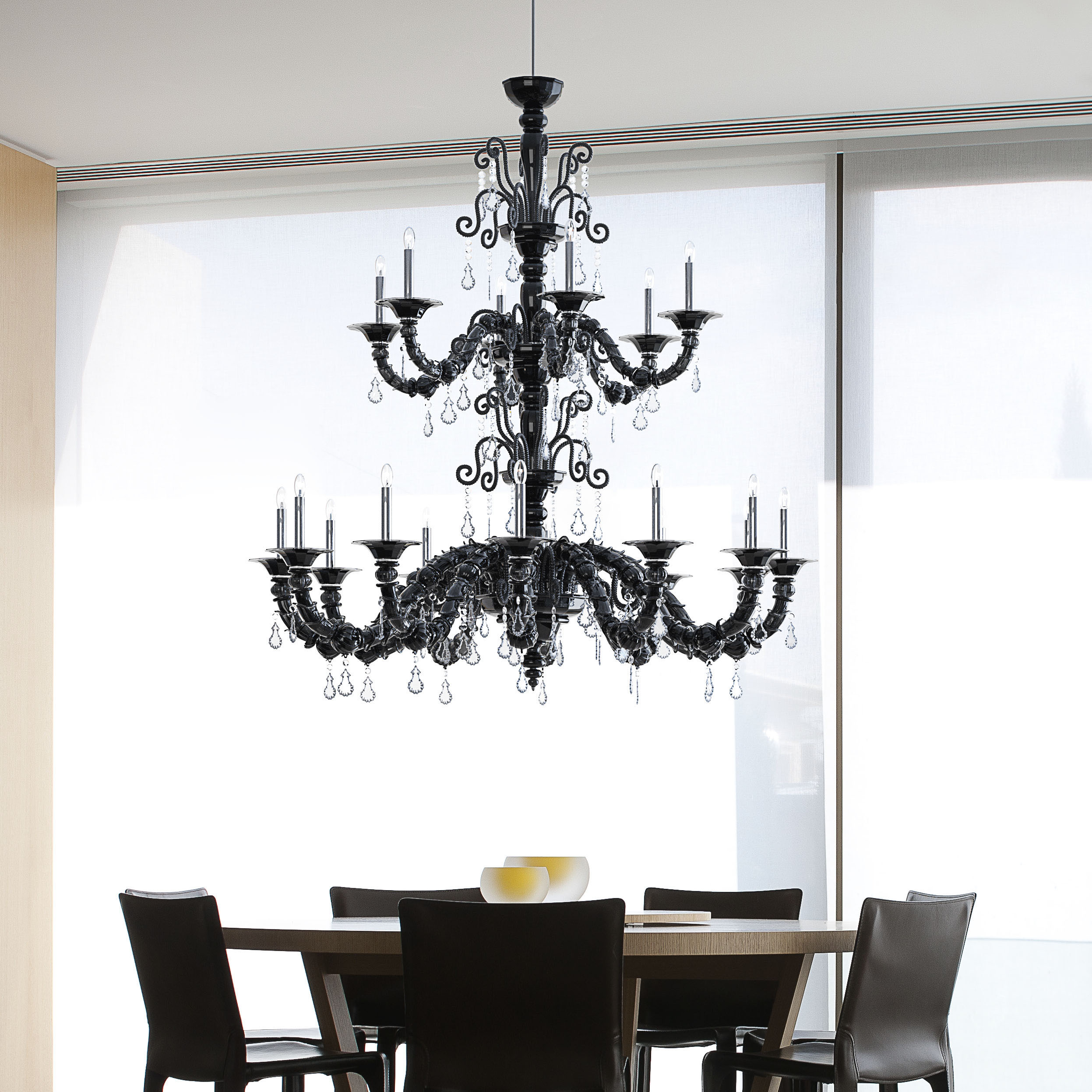
By transforming perceptions of Murano glass from practicality to fine art, Ercole cemented Barovier&Toso’s timeless appeal. It’s why gazing upward at chandeliers in museums, palaces, and luxury boutiques inspires similar wonder: the crystalline glassworks dangling from these peaked ceilings were made by the same family with the same time-honored (and timeless) techniques.
Today, these showpieces grace renowned collections including those at the Louvre, Victoria & Albert Museum of London, and New York’s Corning museum, plus lobbies of Ritz Carlton and Four Seasons properties and the boutiques and homes of Dolce & Gabbana – yes, the Domenico Dolce and Stefano Gabbana.
In the 1980s, one of Barovier&Toso’s most iconic and frequently replicated designs was commissioned for the home of a Saudi King. The Taif chandelier fuses classical elements of Murano glassmaking with futuristic colors and accents to create an everlasting piece that’s simultaneously traditional and contemporary. The first ever black crystal–created by using the darkest burgundy hue possible–continues to set these chandeliers apart, as do bright blue, orange, and ruby red versions of the Taif.
In 2015 Barovier&Toso entered a new era, transitioning ownership from Jacopo Barovier to Rinaldo Invernizzi, a local art collector and painter–passing the leadership torch to the first non-Barovier in history. A devoted designer himself, Invernizzi appears to be a natural fit for Barovier&Toso’s art-driven ethos.
Recently, we had the good fortune of catching up with Barovier&Toso’s CCO, Diego Martinez Dubosc, to talk about the brand’s latest chapter.
What is the company’s design philosophy/mission statement?
Barovier&Toso’s design philosophy and mission statement has evolved over time, but historically, our approach has been characterized by a commitment to craftsmanship, innovation, and timeless beauty. We have strived to combine traditional glassmaking techniques with contemporary design concepts, creating unique and luxurious pieces of glass art.
The company’s mission has been to uphold the legacy of Murano glass and push the boundaries of what is possible with this ancient craft. We have aimed to create objects that are not only visually stunning but also showcase the technical mastery and artistic expression of our artisans.
Our designs often combine exquisite craftsmanship, attention to detail, and a commitment to quality, resulting in luxurious and elegant lighting fixtures and glass artworks. Barovier&Toso is known for pushing the boundaries of glass artistry, experimenting with shapes, colors, and textures to create unique and distinctive pieces.
What sets a Barovier&Toso piece apart from other Murano glasswork?
The product should inspire emotionally; it should have quality, reflect creativity, beauty. Quality that lasts and is passed on from generation to generation, aesthetics and unique design that creates an emotional connection between the product and the consumer, rarity to create ‘objects of desire’, symbolism (luxury products and spaces include a high level of symbolism such as charisma, perfection, style..) and heritage built on traditions and craftsmanship.
A Barovier&Toso’s creation is a form of art and culture, going beyond the material use of it as a lighting appliance to a style, an ambience, and a perceptible emotion. Choosing such a piece of art connotes a deep uncommon sensibility and delightful aesthetic taste.
Creativity, flexibility and know-how attend upon a client that is not satisfied with ready-made and ordinary objects.
What does “Made in Italy” mean to you?
Companies like ours: where all strategic and non-strategic processes are governed internally. We rely on a few external suppliers, only for some materials and minor processes. In short, our supply chain is light and in any case very short, almost zero kilometers. Furthermore, ours is a handcrafted and made-to-measure product, therefore we produce according to orders.
To then move on to a more cultural level, the value of the brand and the “made in Italy” label will certainly become even more important, which is a guarantee and synonym of the quality of the project, of the materials used, of the production process in its entirety in respect of the territory and human capital. We will continue to focus on insourcing, already our distinctive feature, to internally control all stages of production, I would say almost obsessively, in order to be able to offer a truly excellent product.
What is the design and manufacturing process for a Barovier & Toso fixture? From start to finish, how long does it usually take to craft a light fixture for the Barovier&Toso team?
Long and meticulous, the process that leads to the creation of a Barovier&Toso work is divided into multiple stages. The glass mass is worked and shaped by expert hands, thanks to the help of a series of work tools. They are tools handed down from generation to generation, who have known Venetian crystal for centuries. Each of them has a specific function and is essential for re-proposing traditional techniques. The master carries out many processes by hand (freehand) but often the blowing also takes place with the aid of wooden or cast-iron molds or the glass is poured into containment masks for the realization of the glass in plate.
Producing by hand means modeling the material that will compose the final artistic product in all its parts, including every smallest detail. For this reason, the master glassmaker will employ longer times and phases than the big industry, with a greater commitment in terms of physical effort and with the possibility of having to make corrections during the creation of the object.
Each chandelier is different from all the others, but to give you an idea a Taif chandelier with 12 bulbs is made with 100kgr of sand that correspond to 160kgr of molten glass. It takes 3750 minutes in the furnaces, 900 minutes of grinding and assembling and 130 minutes of quality control and packing.
The post Barovier&Toso: Over 700 Years of Italian Design Tradition first appeared on The Edit: The Lumens Content Library.
[ad_2]
www.lumens.com